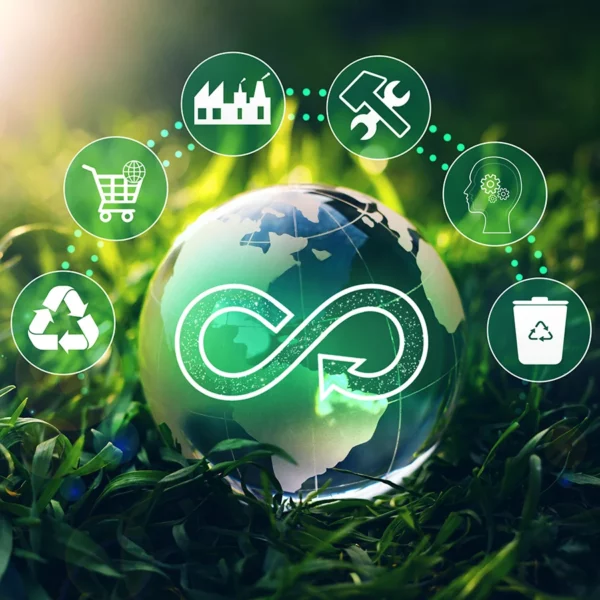
Dans cet article, nous explorons en détail le fonctionnement des taxes et éco-contributions, leur impact sur les entreprises et comment un ERP performant peut simplifier leur gestion au quotidien.
Depuis quelques années, l’industrie vit une nouvelle révolution portée par des technologies de rupture comme l‘Internet des objets (IoT), l‘intelligence artificielle (IA), le cloud computing ou encore la réalité augmentée (AR). Cette industrie 4.0, aussi appelée industrie du futur, promet des gains significatifs de productivité et de flexibilité grâce à des usines plus connectées, plus intelligentes et plus agiles.
Dans ce contexte, la maintenance évolue elle aussi à grands pas. Hier encore curative (réparer après la panne) ou préventive (entretenir selon un calendrier), elle devient aujourd’hui prédictive grâce à l’analyse en temps réel des données issues des machines. Cette maintenance prédictive s’impose comme une composante essentielle de l’industrie 4.0, permettant d’anticiper les défaillances, d’optimiser les interventions et in fine d’améliorer la performance globale des outils de production.
Métier
11 octobre 2024 –
13 mn de lecture
La maintenance prédictive consiste à anticiper les pannes des équipements industriels avant qu’elles ne surviennent, en analysant en continu leur état de santé. Concrètement, de multiples capteurs (vibrations, température, pression, etc.) sont installés sur les machines pour collecter des données reflétant leur fonctionnement. Ces données sont transmises en temps réel vers des plateformes cloud sécurisées où elles sont traitées par des algorithmes d’intelligence artificielle capables de détecter des anomalies et de prédire les défaillances à venir.
L’objectif est d’intervenir au bon moment, juste avant la panne, pour remplacer ou réparer les composants usés. Et ce de façon ciblée, sur les équipements qui en ont réellement besoin. Il s’agit donc d’une maintenance conditionnelle, qui s’adapte en permanence à l’état réel des machines, et non d’une maintenance systématique réalisée à intervalles fixes. Cela permet d’optimiser à la fois les coûts, les délais et la qualité des interventions.
La maintenance prédictive se distingue des approches traditionnelles que sont :
Avec la maintenance prédictive, on passe d’une logique de réaction ou de planification à une logique d’anticipation qui s’appuie sur l’exploitation des données terrain. Les interventions ne sont plus déclenchées sur une base temporelle arbitraire mais en fonction de l’état réel des équipements et d’une prévision de leur évolution dans le temps. Cela suppose de surveiller un grand nombre de paramètres et d’être capable de modéliser des phénomènes complexes grâce à l’IA.
L’intelligence artificielle (IA) est au cœur de la maintenance prédictive. Les algorithmes de machine learning analysent les données collectées par les capteurs pour détecter des anomalies et prédire les pannes. Par exemple, un algorithme peut apprendre à partir de données historiques et en temps réel pour identifier des schémas de défaillance et estimer la durée de vie restante des composants. L’IA permet également d’optimiser les interventions de maintenance en fonction de l’état réel des équipements, ce qui réduit les coûts et améliore la disponibilité des machines. Par exemple, une entreprise de production peut utiliser l’IA pour provoquer des interventions de maintenance sur des périodes de faible activité, minimisant ainsi l’impact sur la production.
Le big data joue un rôle clé dans la maintenance prédictive en permettant de traiter et d’analyser de grandes quantités de données collectées par les capteurs. Les données historiques et en temps réel sont utilisées pour construire des modèles prédictifs qui permettent de planifier les interventions de maintenance de manière optimale. Par exemple, les géants industriels GE et Rolls-Royce exploitent l’intelligence artificielle pour la maintenance prédictive des moteurs d’avion, analysant les données en temps réel pour détecter les problèmes potentiels et planifier la maintenance nécessaire. Cette approche permet d’améliorer la sécurité, l’efficacité et la performance environnementale des moteurs, tout en optimisant les calendriers de maintenance.
L’Internet des objets (IoT) permet la collecte de données en temps réel à partir de capteurs installés sur les équipements. Ces capteurs peuvent mesurer une variété de paramètres tels que la température, les vibrations, la pression, et bien d’autres encore. Les données collectées sont ensuite transmises à des plateformes cloud où elles sont analysées pour détecter des anomalies et prédire les pannes potentielles. C’est la combinaison de l’IoT, du cloud et de l’IA qui permettent d’aboutir à la maintenance prédictive. Par exemple, l’ascensoriste KONE installe des capteurs IoT sur ses ascenseurs et les données sont traitées par l’IA qui les analyse en temps réel, permettant de détecter proactivement les problèmes potentiels et de planifier les interventions nécessaires. Ce système améliore la rentabilité, la durée de vie des équipements et la sécurité des usagers, avec des résultats impressionnants : jusqu’à 50% d’interventions en moins après un an et 95% des défaillances potentielles identifiées de manière proactive dès la première année.
La réalité virtuelle (VR) et la réalité augmentée (AR) sont des technologies prometteuses pour la maintenance prédictive, offrant des avantages significatifs en termes de visualisation, de formation et d’efficacité des interventions.
La réalité virtuelle (VR) permet aux techniciens de visualiser les équipements en trois dimensions dans un environnement virtuel immersif. Cela leur permet d’explorer virtuellement les machines, d’identifier les composants qui nécessitent une maintenance et de simuler des interventions avant de les réaliser sur le terrain. Par exemple, un technicien peut naviguer à l’intérieur d’une turbine complexe, examiner les pièces internes et planifier les étapes de la réparation sans avoir à démonter physiquement l’équipement.
La réalité augmentée (AR), superpose des informations numériques en temps réel sur l’environnement physique. En utilisant des lunettes AR ou des tablettes, les techniciens peuvent voir des instructions de maintenance, des schémas techniques et des données de capteurs directement sur les équipements qu’ils réparent. Cela réduit les risques d’erreurs en fournissant des indications précises et en temps réel, et améliore l’efficacité des interventions. Par exemple, lors de la réparation d’une machine, un technicien peut être accompagné en visualisant des flèches et des annotations superposées sur les composants, indiquant les étapes à suivre et les outils à utiliser.
Ces technologies peuvent se combiner et deviennent la réalité mixte (MR), voire la Réalité Étendue (XR, eXtended Reality) qui désigne toutes les formes de réalité qui combinent des éléments physiques et numériques. Lors des interventions à distance, des experts peuvent guider les techniciens sur le terrain depuis n’importe quel endroit, grâce à un casque connecté.
De plus, cette technologie permet une formation plus immersive et interactive, accélérant l’apprentissage et améliorant la rétention des connaissances.
En résumé, ces technologies, en pleine ascension, jouent un rôle crucial dans la maintenance prédictive en améliorant la visualisation des équipements, en réduisant les erreurs, en augmentant l’efficacité des interventions et en offrant des possibilités de formation avancées.
Le premier bénéfice de la maintenance prédictive est économique. En intervenant au bon moment, avant que la panne ne survienne, on évite les coûts et les pertes de production liés aux arrêts non planifiés. Selon une étude de McKinsey, la maintenance prédictive permettrait de réduire les coûts de maintenance de 10 à 40% et les temps d’immobilisation des équipements de 50%.
Prenons l’exemple d’un centre d’usinage dont la broche, qui fait tourner à grande vitesse l’outil de coupe, est sur le point de casser. Avec une maintenance traditionnelle, la panne surviendra de façon soudaine avec un risque pour la pièce métallique en cours de production, nécessitant l’arrêt total de la machine pendant plusieurs jours, le temps de diagnostiquer le problème, de commander la pièce et de la remplacer. Soit un coût significatif en termes de main d’œuvre, de pièces et surtout de perte d’exploitation.
Avec une maintenance prédictive, les vibrations anormales de la broche seront détectées à l’avance, permettant de planifier son remplacement sur un créneau d’arrêt programmé, sans perturber la production. On passe d’une logique réactive et subie à une logique proactive et maîtrisée, source d’importantes économies.
En surveillant l’état de santé des machines en continu, la maintenance prédictive permet d’optimiser leur durée de vie. Concrètement, on ne remplace plus systématiquement les composants selon un calendrier prédéfini, mais seulement lorsque c’est vraiment nécessaire, en fonction de leur niveau d’usure réel. Cela évite de changer des pièces encore fonctionnelles et de faire des dépenses inutiles.
De plus, les algorithmes de maintenance prédictive sont capables d’estimer précisément la durée de vie résiduelle (RUL) des équipements, c’est-à-dire le temps pendant lequel ils peuvent encore fonctionner avant la défaillance. Une information précieuse pour anticiper les commandes de pièces de rechange et les interventions. Selon une étude de Deloitte, le temps de fonctionnement et de la disponibilité des équipements augmenteraient de 10 à 20%.
En permettant d’intervenir sur les équipements avant qu’ils ne dérivent, la maintenance prédictive a aussi un impact positif sur la qualité des produits fabriqués. Les machines qui fonctionnent de façon optimale, sans à-coups ni défauts, donnent de meilleurs résultats en termes de précision, de régularité et de performance. C’est particulièrement critique dans des secteurs comme la pharmacie, l’agroalimentaire, la mécanique ou l’automobile, où le moindre écart peut entraîner des conséquences majeures.
Autre enjeu : la sécurité. En détectant les anomalies naissantes, la maintenance prédictive permet d’éviter les pannes soudaines qui peuvent mettre en danger les opérateurs ou l’environnement. C’est le cas par exemple dans les usines chimiques, les centrales nucléaires ou les plateformes pétrolières, où les défaillances d’équipements critiques peuvent avoir des conséquences catastrophiques. La maintenance prédictive s’inscrit donc dans une logique de maîtrise des risques industriels.
La maintenance prédictive permet aussi d’optimiser la gestion des ressources humaines et matérielles. Côté main d’œuvre, les interventions étant mieux anticipées et ciblées. Les techniciens opèrent des actions de maintenance parfaitement définies et maitrisées sans perte de temps. Ils peuvent se concentrer sur des tâches à plus forte valeur ajoutée comme l’analyse des données, le diagnostic ou l’amélioration continue. Cela valorise leurs compétences et leur engagement.
Côté pièces détachées, la connaissance précise de l’état des équipements et l’anticipation des défaillances permettent de commander les composants au bon moment, sans risquer de rupture de stock ni d’immobilisation des machines. Cela réduit les coûts de possession tout en garantissant la disponibilité des pièces. De plus, l’historique des données collectées aide à mieux comprendre les mécanismes d’usure et à optimiser le choix des fournisseurs et des matériaux.
La maintenance prédictive s’impose comme une composante essentielle de l’industrie 4.0, permettant d’anticiper les défaillances, d’optimiser les interventions et d’améliorer la performance globale des outils de production. Les technologies telles que l’IoT, la VR, l’IA et le big data jouent un rôle crucial dans le futur de la maintenance prédictive.
Selon une étude McKinsey, la maintenance prédictive pourrait bénéficier aux fabricants principalement de trois manières :
Malgré les obstacles à surmonter, la dynamique actuelle devrait s’intensifier dans les années à venir, grâce à la maturation des technologies et à la pression de la concurrence. L’adoption de la maintenance prédictive devrait connaître une augmentation significative au cours de la prochaine décennie. Aujourd’hui estimée à environ 10 %, cette adoption pourrait atteindre entre 55 et 70 % d’ici 2030 !
L’ERP, qui centralise les données de l’entreprise, et la maintenance prédictive se complètent et sont indissociables pour optimiser la bonne planification des OF, des interventions de maintenance, gérer les stocks de pièces de rechange et réduire les coûts. La combinaison des deux dans une usine interconnectée permet de maximiser la disponibilité des équipements, d’améliorer la productivité globale et de maintenir un haut niveau de performance opérationnelle.
Dans cet article, nous explorons en détail le fonctionnement des taxes et éco-contributions, leur impact sur les entreprises et comment un ERP performant peut simplifier leur gestion au quotidien.
Et si on changeait de regard sur la dématérialisation des factures ? Elle représente bien plus qu’une simple obligation légale ; c’est une opportunité pour les entreprises de digitaliser leurs processus, améliorer leur efficacité opérationnelle et renforcer leur compétitivité.